-
- Some services are not accessible on a smartphone.
- Sign In
- My Account
- My Cart
- Customer Service
- Bindery Parts & Equipment | Finishing Parts Equipment | Bindery Supply
- >Meech Static Control Applications for Plastic
Alignment Of Parisons During Small Bottle Manufacture

In extrusion processes, closely spaced small extrusion heads often lead to significant parison deflection and reduced yield. This is primarily due to the mold pinching the parisons. Additionally, the restricted space around the extrusion heads and at the top of the mold creates a challenge for effective ionization delivery to the parisons, as the proximity to the earth forms a barrier.
Solution:
To address this, Meech suggests the implementation of the 261 Flexi Nozzles. These nozzles are designed to emit a stream of ionized air between the parisons. This approach effectively reduces parison deflection without causing any cooling effect on the parison itself. The compact design of the 261 Nozzle enables its strategic placement above the mold tool. From this position, it can direct airflows along the length of the parisons, minimizing their contact with the mold tool. This innovative solution has successfully facilitated the production of small double-cavity containers. Previous attempts using ionized air curtains and ionizing bars were less effective, as they failed to adequately penetrate the space between the mold tool and the parisons.
![]() |
261 Flexi Nozzles |
CD & DVD Delamination During Manufacture

Problem:
A DVD is created by combining two CDs, which are bonded using a unique adhesive. However, due to the similar polarity charges of the disks, bonding can be imperfect, leading to pinholes.
Solution:
To resolve this issue, one of the disks can be charged with the opposite polarity using a 993R Bar, resulting in flawless bonding.
![]() |
993R Bar |
Cleaning UPVC Profile Extrusion After Machining Or Pre Decoration
Problem:
Profiles that are warm and highly charged accumulate significant amounts of swarf following the sawing process, leading to several problems:
- Operators experience painful electric shocks, which negatively impacts their morale
- Accumulation of charged swarf on the machinery and surrounding work area
- Difficulty in painting or applying foil wrap due to swarf adhering to the profile lengths
- Swarf, attracted by static, spreads to other areas, causing unwanted contamination
Solution:
The strategic placement of 957 ionizing air curtains can effectively remove and neutralize the swarf while also neutralizing the profile. This ensures a clean, static-free section at the end of the extrusion line.
Additionally, implementing a barrier at the saw box extraction system can improve its efficiency and prevent the spread of contamination to the broader work area.
![]() |
957 ionizing air curtains |
Contamination Control For Door Seal Manufacturing
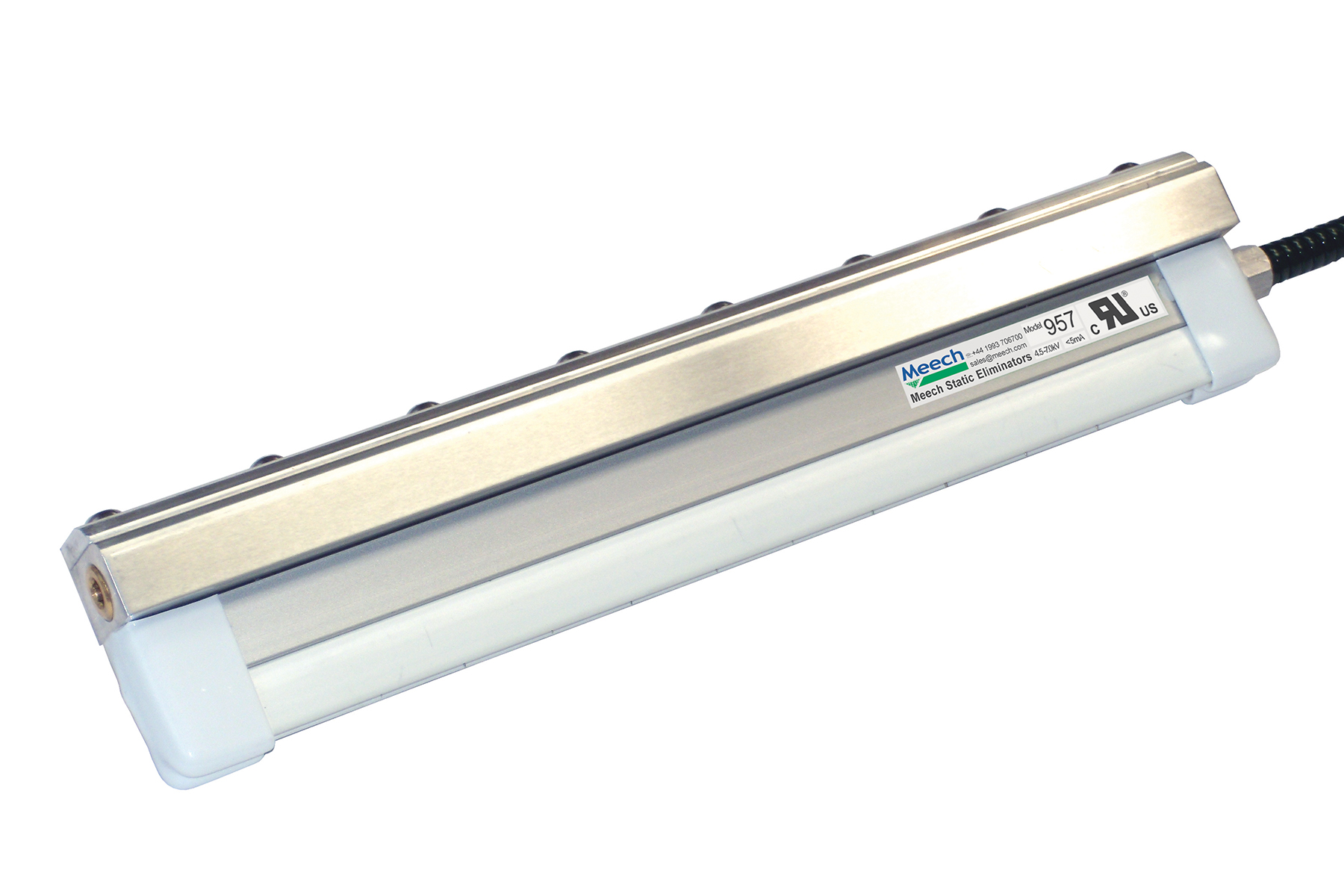
Problem:
In the automotive industry, extruded rubber used for applications like door seals faces contamination challenges. The stringent quality standards set by manufacturers often lead to batch rejections and potential penalty claims.
Solution:
Employing a Meech 957 ionizing air curtain is effective in addressing this issue. It aids in cooling while simultaneously neutralizing electrostatic charges, thereby mitigating contamination risks.
![]() |
Meech 957 ionizing air curtain |
Contamination Control in Thermoforming
Problem:
Sheet materials must be devoid of contamination and plastic swarf before being fed into the thermoforming machine. Neglecting to ensure the cleanliness of these materials can lead to inclusions in the final product.
Solution:
For cleaning large sheets, the Meech JetStream Ionizing Air Knife System is suitable, whereas smaller sheets can be effectively cleaned using either a Meech 957 air curtain or a Meech 954 ionizing gun. Additionally, charges generated during the thermoforming process might cause more contamination or result in electric shocks to operators during handling.
![]() | ![]() | ![]() |
JetStream Ionizing Air Knife | Meech 957 air curtain | Meech 954 ionizing |
Contamination Control on Injected Molded Products
Problem:
During the injection molding process, and as products cool, electrostatic charges accumulate. These charges attract contaminants from the conveyor and the surrounding environment onto the products. This issue becomes more pronounced in productions involving In-Mold Labelling (IML).
Solution:
By installing a Meech 971IPS bar at the end of the conveyor, near the robot set-down area, products can pass through its ionizing field. This neutralizes the surfaces of the products. Additionally, as the product cools while on the conveyor, the continuous ion flow from the bar helps control any reformation of electrostatic charges.
![]() |
Meech 971IPS bar |
Conveying Plastic Granules Activating Metal Detector
Problem:
In the plastic industry, the production of plastic granules involves an extrusion process before they are cut into the necessary sizes. During the process of moving these granules through ducting, electrostatic discharges occur. These discharges inadvertently trigger the metal detector, leading to the disposal of the product into the reject bin.
Solution:
The optimal remedy for this issue is to implement an inline static control. This can be effectively achieved by integrating a Meech 913 flow tube just before the metal detector. This setup ensures the reduction of electrostatic discharges, thereby preventing false alarms in the metal detector and avoiding unnecessary product wastage.
![]() |
Meech 913 |
Conveyor Problems With Plastic Blow-Moulded Bottles
Problem:
When transporting blow-molded plastic containers (like shampoo bottles) on a conveyor, they accumulate significant static electricity. This static charge draws dust, leading to contamination levels that are not acceptable.
Additional issues include the necessity for extra cleaning at the pre-filling stage, elevating production costs, and a heightened risk of electric shocks to workers, which poses health and safety concerns.
Solution:
Implementing either the model 971 or 929IPS Hyperion Bar can effectively mitigate static charge accumulation.
These Meech Hyperion Bars emit continuous ion streams, neutralizing static on the blow-molded bottles, conveyor, and even the workers (through their hands and arms) when they are within the ionization field.
Typically, they are installed above the conveyor on an elevated gantry, similar to a strip light fixture.
![]() | ![]() |
Model 971 | 929IPS Hyperion Bar |
IML Decoration Of Plastic Molds Using Static Pinning
Problem:
During the in-mold labeling process, it's crucial to accurately position and secure the label inside the mold tool. Relying on tabs or recesses for this task can be challenging and inconsistent. Any displacement of the label during the process may result in the rejection of the final product.
Solution:
Using static electricity to stick the label inside the mold makes the process simpler and keeps the label in place temporarily. A robot arm picks up the label and either uses a static bar to charge it before placing it in the mold or directly sticks it onto the mold. This can also be done by hand. After the label is attached to the mold, the robot arm moves back, the mold closes, and plastic is added, creating a container with the label already on it.
Moldings Sticking to Tool Face During Injection Molding
Problem:
Small and lightweight moldings may adhere to the tool surface because of static electricity. This can lead to damage to the mold and reduce the speed of production.
Solution:
Placing a Meech Model 959IPS either above or beside the problem area can eliminate static charge, assisting in the removal of parts. To conserve air and prevent unnecessary cooling of the mold tool, air can be pulsed through the air curtain only when the tool is open.
![]() |
Meech Model 959IP |
Neutralising Static Generated While 3D Printing
Problem:
Static electricity on the model powder during printing can mix it with the support material, leading to a bad finish or a weaker structure because filler gets into the molded product.
The UV light hardens very thin layers, one after the other. The static created during this hardening pushes the powder away as it prints.
Solution:
Using a Meech 929IPS bar to neutralize the mold between each pass helps control static charges, which prevents the powder from being pushed away.
![]() |
Meech 929IPS bar |
Operator Shocks During Electrical Cable Manufacturing
Problem:
The plastic coating on the conductors can cause health and safety concerns because of the risk of electrostatic shocks. Static electricity accumulates in the conductors, leading to sudden releases of high-voltage energy when handled by workers.
Solution:
Neutralizing the coated wire while it's being rewound helps manage the build-up of static charge. Employing the Meech 929IPS bar is effective for this control.
![]() |
Meech 929IPS bar |
Operator Shocks In Tyre Manufacture
Problem:
When rubber is extruded onto a carrier belt to cool, its separation from the carrier creates large static charges, which can lead to health and safety concerns.
Solution:
The use of a Meech 971 system or 935 system dependent on the available positioning will offer the most effective solution.
![]() |
Meech 971 |
Print Quality Problems With Ink Jet Printing On UPVC Extrusion
Problem:
During the extrusion process of uPVC profile, high voltage static charges cause several issues for inkjet printing systems:
- Dust is attracted to the surface that's being printed on
- The inkjet is deflected, which leads to poor print quality
- Too much ink is drawn to the surface, causing feathered edges
- The inkjet printing equipment may experience electronic failures
- The directional deflector plate gets contaminated, resulting in production downtime for cleaning
Solution:
Placing a strong Model 915 ionizing bar before the print head neutralizes the static charge, ensuring:
- No dust is attracted
- Improved print quality - no feathering or ink deflection
- Prevention of electrostatically induced electronic failures
- A clean directional deflector plate leads to less cleaning and better productivity
This principle works for other surfaces that need inkjet printing.
Note: A Model 940BE nozzle can be used as an alternative to a Model 915 ionizing bar.
![]() |
Model 915 ionizing bar |
Static Problems Causing Blow Moulding Parison Misalignment
Problem:
When molten plastic parisons fall into an open mold, high static charges lead to issues:
- If there's more than one parison per mold, they all have the same charge and repel each other. This often leads to unsuccessful placement into the mold and quality issues like stress lines in the final product.
- With a single parison, similar problems arise if it gets attracted to any of the metal parts of the machine.
Solution:
The Meech models 971 or 971IPS provide extensive, long-range ionization without needing an air delivery system. The ions spread from these systems completely neutralize static from the parison extrusion head to the top of the mold tool. This is especially effective for very thin parisons that can be easily cooled or misdirected by even the slightest airflow.
Where space is tight a 929IPS bar is a good alternative.
![]() | ![]() |
Meech 971 | Meech 29IPS |
Swarf & Contamination Control On Extruded Plastics
Problem:
Static charges build up on extruded tubes as they cool. Using a water bath grounds the charges on the outside, but drying and machining regenerate stronger charges.
This leads to swarf and environmental contaminants sticking to the product's surface.
Such contamination can cause issues during printing, laminating, and finishing processes. Additionally, swarf abrasion during storage is another manufacturing concern.
Solution:
Neutralizing static charges on the tubes will eliminate the risk of electrostatic attraction of contaminants from the surrounding area. An example of this is the use of a Meech 957 air curtain, which not only aids in cooling but also in neutralizing static.
![]() |
Meech 957 air curtain |
Controlling Static Charges In Air Conveyer Diverter Valves
Problem:
Static electricity buildup during the conveyance of waste film or granules may lead to the diverter valve jamming or becoming obstructed, as the product adheres to the gate.
Solution:
Installing Meech 261 Bulkhead nozzles onto the tube will effectively eliminate static charges.
![]() |
Meech 261 Bulkhead nozzles |
Static Control During Film Rewinding
Problem:
The process of winding film on extruded or blown film lines generates significant levels of static electricity, frequently exceeding 200 kV. This can result in several significant issues:
- Operators may experience painful and discomforting shocks
- Elevated static levels within the reel can lead to production issues for the customer
- Dust accumulation from distances of up to 1 meter can occur, potentially contaminating the film
Solution:
The appropriate choice of equipment will be influenced by factors such as machine design and space limitations. The Model 935 fan-driven ionized air blower provides a substantial volume of concentrated ionized air to the winding area. The gentle dispersion of ionized air from the blower head ensures broad coverage and effective neutralization over long distances. This long-range ionization capability ensures comprehensive neutralization of the entire film roll. Additionally, fan filters are accessible to guarantee that only clean air is directed toward the film.
Static Pinning Film On To A Cast Film Extrusion Chill Roller – 995 Claw
Problem:
The cast plastic film emerges from the die in a semi-molten and hot condition, landing directly onto a chill roller. As it gradually cools on the roller, it undergoes a phenomenon known as 'Necking', wherein it contracts in width.
Unfortunately, this necking effect is undesirable as it results in an uneven finished film, thus compromising its quality.
Historically, compressed air jets were employed to maintain the edges of the plastic at the desired width. However, this method proved to be costly, noisy, and often resulted in excessive marking on the film.
Solution:
A more effective solution involves using static electricity to hold the edges in place. The Meech 995-CLAW is specially designed for this purpose.
It consists of pinning heads mounted on either side of the film. Each head has a 25mm diameter mounting rod for easy attachment with standard industrial clamps. These heads offer lateral and rotational adjustment. Three flexible titanium pins can be arranged according to the needs of the application. Each pin is independently resistively coupled, providing strong pinning without risking damage to the roller, which is usually quite costly. The use of extended pins gives the operator more space to work when setting up the film at the beginning of a production run.
Typically, a compressed air gun is initially used to adjust the film to the desired width. Once set, the pinning head pins are activated to hold the film in place. Ideally, there should be a dedicated static generator on each side of the roller, allowing independent manipulation and pinning of both edges.
Meech recommends pairing the 995-CLAW with a 30KV 992v3 negative generator. Its built-in remote on/off control makes operation simpler, allowing the generator to be easily switched on near the pinning head with a simple switch.
Setting Up
It's crucial to use the minimum amount of charge necessary to keep the film's edge in place. If you add too much charge, the film will stick excessively to the cold roller.
Excessive static charge can cause the film to follow a wavering path when removed from the roller, leading to distortion. The more force required to separate the film from the roller, the higher the chance of an uncontrolled release.
Additionally, applying too much charge can increase the tension of the film on the roller, risking stretching, especially if the film isn't fully cured. This stretching becomes apparent during rewinding, resulting in poor roll edges.
The electrostatic charges accumulated in the film can stack on top of each other during rewinding, causing the film to the telescope and resulting in poor edge finishing. To avoid this, it's recommended to neutralize these charges during the rewinding process.
Recommendations
- Arrange the pins in a straight line, evenly spaced from the material they're securing.
- Apply the least amount of power needed to keep the film in place.
- Maintain a distance of 10-15mm between the pins and the film surface. This allows for a gentler charge spread across a larger area, minimizing the chance of material distortion.
- Neutralize the film before rewinding to prevent issues.
![]() |
Meech 995-CLAW |