-
- Some services are not accessible on a smartphone.
- Sign In
- My Account
- My Cart
- Customer Service
- Bindery Parts & Equipment | Finishing Parts Equipment | Bindery Supply
- >Takk Static Control Applications for Plastics
Static Elimination in Plastics Processing
TAKK static eliminators ensure a uniform spread of ionized air during slitting, sheeting, unwinding, rewinding, laminating, and coating processes. By doing so, they prevent static electricity issues, such as frequent personnel shocks, as well as problems like jamming, clinging, and sticking of materials during processing. These issues are commonly encountered with the papers and films used in converting and packaging.
Bag Wicket
Excessive static charges can make bags stick together or push apart in a stacked arrangement. This leads to inefficient stacking, lowering production output, and increasing rejects. To address this issue, installing static eliminators at the entry point, on the wickets, and at the stack ensures that individual bags and the stacked arrangement are fully neutralized, allowing for proper stacking.
Recommended Solutions:
![]() | ![]() |
IonStorm XR2 | 400T Ionizing Bar |
Slitting
While unwinding, pulling the web from the roll creates a static charge that intensifies when the material separates, moves across rollers, and gets slit. This static charge can make layers repel each other during rewinding, leading to lower roll quality.
To prevent contamination and ensure high-quality rolls, install a static eliminator before rewinding to neutralize the charge.
Recommended Solutions:
![]() | ![]() | ![]() |
IonStorm XR2 | Curtain-Air Ionizer | Vortex Ionizer Blower |
Sheeting
In fast processes like sheeting, speed, friction, and separation create static. During sheeting, individual sheets are drawn to the machine and repel each other during stacking.
To improve stacking, reduce jams and downtime, and boost productivity, install a static eliminator above and immediately after the sheeting operation to neutralize the static charge.
Recommended Solutions:
![]() |
400T Ionizing Bar |
Winding
During the winding operation, as the web is pulled from the roll and the material separates a static charge is created. This static attracts airborne dust and contaminates causing rejects, waste, and operator shocks.
On both unwind and rewind applications, installing a static eliminator on top of the roll will neutralize the charge and prevent contamination and shock.
Recommended Solutions:
![]() | ![]() | ![]() |
IonStorm XR2 | Curtain-Air Ionizer | Vortex Ionizer Blower |
Blow Molding
When the plastic parison comes out of the die and enters the open mold, strong static charges make it stick to the grounded metal mold. With multiple die heads, the parisons repel each other, leading to poor product quality and more rejects
To prevent quality issues, install a static eliminator as the plastic is extruded and enters the mold to neutralize the charge.
Recommended Solutions:
![]() | ![]() | ![]() |
IonStorm XR2 | 400T Ionizing Bar | Curtain-Air Ionizer |
![]() | ![]() | ![]() |
Vortex Ionizer Blower | Precision Point Ionizer | Precision Point with Air Nozzle |
Film Extrusion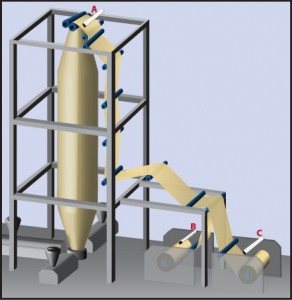
Static charges accumulate as the blown film cools and moves across rollers towards the wind-up, attracting dust and contaminants and causing shocks to operators.
To prevent slowdowns rejects, and operator shocks, as well as to enhance product quality, it is advisable to install static eliminators at the extrusion point and during the winding operation to neutralize the charge.
Recommended Solutions:
![]() | ![]() | ![]() |
IonStorm XR2 | 400T Ionizing Bar | Curtain-Air Ionizer |
Injection Molding
At the end of the injection molding process, static is generated as parts drop into a collection container. Although the charge on each part is small, it accumulates into a significant static field as more parts gather in the collection area. This leads to the attraction of dust and contaminants, causing parts to become dirty, and operators may experience shocks.
To address this issue, install a static eliminator at the collection bin to eliminate these charges and prevent contamination.
Recommended Solutions:
![]() | ![]() | ![]() | ![]() |
IonStorm XR2 | Curtain-Air Ionizer | Vortex Ionizer Blower | Ion-Jet Super Air Knife |
Injection Molding (small, lightweight, complex parts)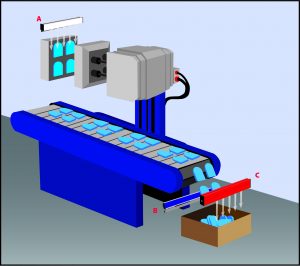
During the injection molding of delicate and lightweight parts for medical, pharmaceutical, and other industries, the parts can stick to the mold ejectors or the injection mold face when the mold is open. Ideally, the parts should easily fall from the mold ejectors onto a conveyor or into a catch bin. However, if static electricity is too high and not controlled, the parts won't fall freely. This can lead to problems such as loss of usable parts, clogged ejectors, potential damage, downtime, reduced productivity, and profit loss.
To solve this issue, using a static eliminator bar with air assist flowing down the mold/mold ejectors' face will eliminate the static electricity and prevent these problems.
Recommended Solutions:
![]() | ![]() | ![]() |
Model 3024 DC Ionizer | 400T Ionizing Bar | Ion-Jet Super Air Knife |
In-Mold Labeling
During the In-Mold Labeling (IML)/Decorating process, placing a product label in a specific mold location is crucial. An efficient method for this is using an electrostatic charging system, consisting of a Static Generator (A) and devices like Charging Bars (B) or Charging Point Pinners.
By applying an electrostatic charge to the label using this equipment, the label easily sticks to the mold's surface. The charge creates a bonding force, ensuring the label stays in place during the molding process.
In the process, the label is picked up, moved over a Charging Bar (B), and put into the mold. The static charge keeps it in position as the mold closes, completing the process. When the mold opens, the label is fused onto the surface of the injection molded object.
Recommended Solutions: